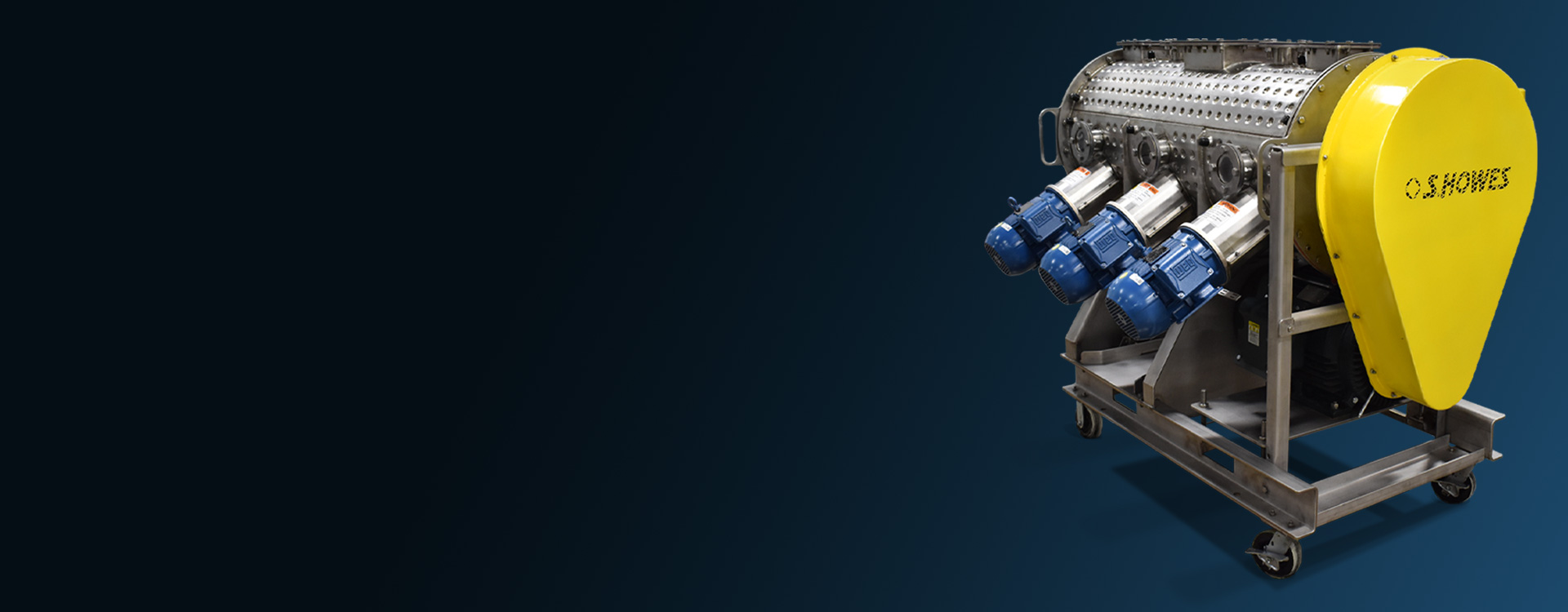
Heating & Cooling For Mixers
Enhanced thermal processing with innovative jacket design for precise temperature control.
Thermal processing is accomplished through a bolt-on or integral external fluid jacket on the mixing vessel. Material is heated or cooled by direct contact with the surface area on the tank walls as the paddles and/or ribbons continuously agitate the material. The jackets can utilize a traditional design where a continuous chamber is added or be built with multiple independent jacket panels to provide more precise temperature control.
Let our engineers design a thermal processing mixer for your heating and cooling requirements.
General Features & Benefits
- Thermal treatment occurs during the mixing cycle and in the same vessel to eliminate secondary process steps and unnecessary additonal equipment.
- Independent jacket configuration allows a parallel feed of fluid to each jacket panel where product is always exposed to a fresh temperature cycle.
- Steam, water or hot oil can be used for thermal treatments and refrigerants can be used for cooling.
- Accurate control of batch thermal treatment time.
- Good control of end material temperature.
- ASME “U” Stamp and “R” Stamp Cerificates of Authorization.
Limits
- Materials that soften on heating (thermoplastic) may smear and foul preventing satisfactory heat transfer.
- Material needs to flow well during thermal treatment period to ensure homogeneous treatment.
- Lower heat transfer coefficients than with convective temperature control.
- Temperature of heat transfer media must be controlled to a point that will not damage the material when the material is in direct contact with thermal surface.
Mixers With Heating & Cooling
Thermal treatment is provided through a thermal fluid jacket on the mixing vessel. Material is heated or cooled by direct contact with the surface area on the tank walls as the paddles and/or ribbons continuously agitate the material. Based on standard models, our engineers can design a heating or cooling mixer to your specific processing needs.
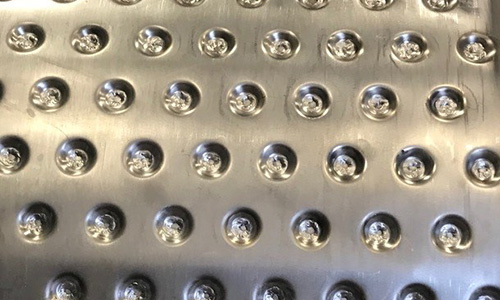
Sample Applications
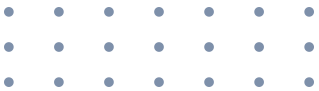
- Drying
- Cooling
- Heat Curing
- Polymerization
- Microbial Kill
- Suitable for a wide variety of bulk solids
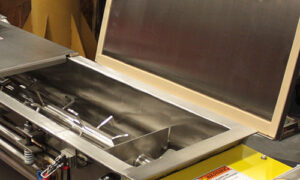
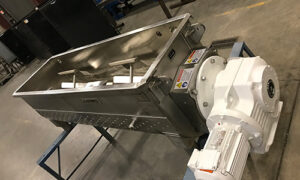
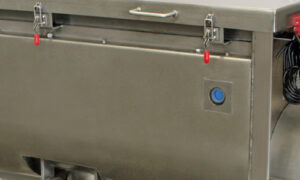
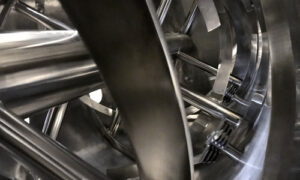
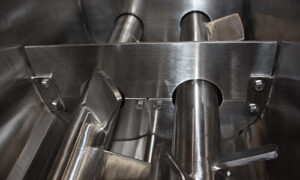
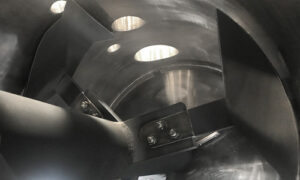
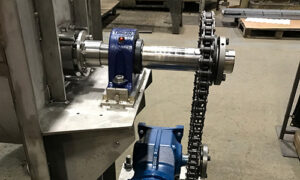
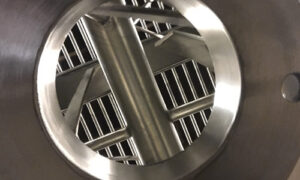
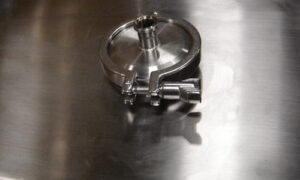
Options & Accessories
- Batch and continuous operation
- Double ribbon, paddle, plough-style and custom agitator designs
- High-velocity intensifiers / choppers
- Variety of access options for inlets, covers and inspection manways
- Temperature sensors, level sensors, limit switches
- Direct, chain, or belt drive
- Gates and discharge options
Downloads
Atmospheric Mixers (Dryers)
Conductive heating of materials through a thermal fluid jacket on the mixing vessel will result in a flash evaporation of volatile components such as water or organic solvents as the material agitation or transfer exposes the material to the open space at the top of the S. Howes mixer. In order to continue to drive the evaporation, the vapor in this free space must be removed either by the assistance of a conventional fan or by convection.
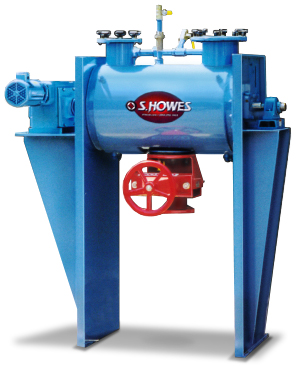
Features & Benefits
- Low capital cost as the drying is accomplished in the same time and vessel being used for transferring and/or mixing.
- Control of batch drying time.
- Good control of end material temperature.
- Suitable for drying of either water or organic solvents.
- No or low dust generation, reduces chances for dust explosions that can occur in convective type dryers.
- Residence time can be adjusted to allow for the removal of “bound” moisture.
Limits
- Generally for heat insensitive materials.
- Thermoplastic (heat softening) may smear and foul preventing satisfactory heat transfer.
- Material needs to flow well during thermal treatment period to ensure homogeneous treatment.
- Lower heat transfer coefficients than with convective dryers.
- Temperature of heat transfer media must be controlled to a point that will not damage the material when the material is in direct contact with thermal surface.
Vacuum Mixers (Dryers)
Similar to atmospheric drying, the vacuum process also reduces the atmospheric pressure within the mixer to reduce the vapor pressure of the water. This allows the evaporation of the volatile component to occur at a lower temperature than at atmospheric conditions. Based on standard models, our engineers can design a vacuum mixer/dryer to your specific processing needs.
Features & Benefits
- Lower operating temperatures make it more suitable for heat sensitive materials such as pharmaceuticals or materials that melt at higher temperatures at atmospheric pressure.
- Head space in the mixer is filled with vapor that will reduce or eliminate presence of oxygen for oxygen sensitive materials or solvents.
- Batch drying time is infinitely variable depending on the residence time required.
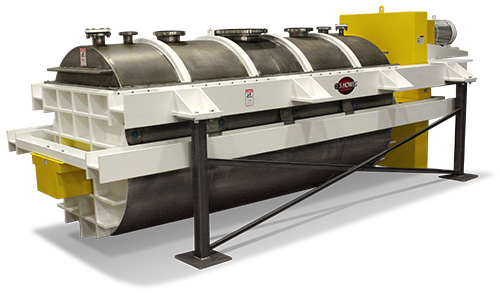
Limits
- More costly since vacuum system must be included.
- More costly as mixer vessel and other components need to be constructed to handle and maintain the vacuum pressure.
- Lower heat transfer coefficients than with convective dryers.
- Temperature of heat transfer media must be controlled to a point that will not damage the material when the material is in direct contact with thermal surface.
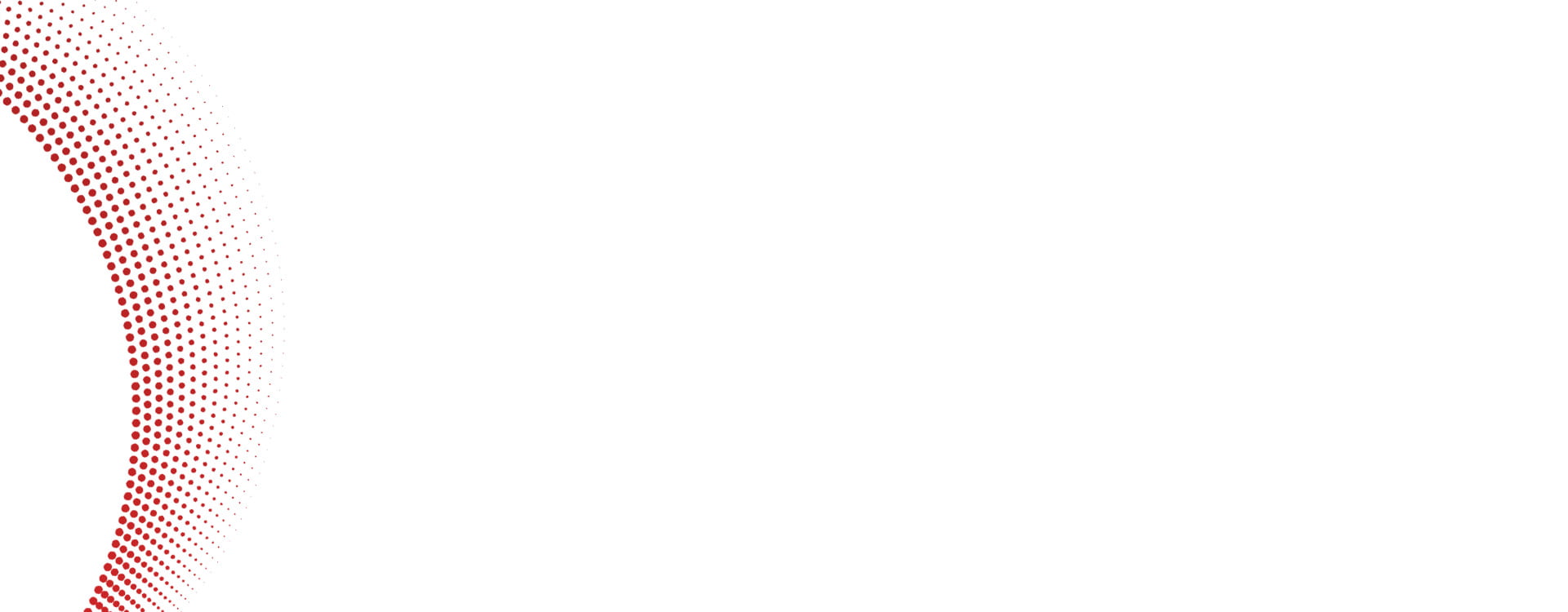
Test Lab & Innovation Center
Your Material Product. Our Thermal Processing Equipment.
Make sure your new process equipment delivers your desired final material requirements.
Lab Testing
Leverage the CPEG Innovation Center and expertise in process engineering to test material product prior to the design or purchase of bulk solids and material handling equipment.
Testing With Rental Units
When material testing in the Innovation Center is not feasible, S. Howes provides rental equipment that can be shipped directly to your site for reliable testing of powder and bulk solids materials.