Food Ingredient Unloading & Conveying System
The Process Challenge
A rubber sheet manufacturer approached S. Howes to help reduce worker back injuries by replacing a manual loading method with a mechanical loading system. The one critical need was that the system be compatible with an explosive environment.
The Solution
The first requirement was to design a cart that could receive an entire batch of material, transport it to the sheeting mill area, and dump it into the receiving hopper of the screw conveyor. A portable dump cart made entirely of aluminum and brass was designed and built for this purpose. The cart could then be rolled to the work area and lifted by the customer’s fork to the proper dump height.
The second requirement was a split tube conveyor to move the product from the receiving hopper to the feed table of the sheet mill. The receiving hopper was sized to accept a full cartload of material. The conveyor was an S. Howes Split Tube Conveyor on a portable base. A control panel was built to provide the operator with an on-demand conveyor operation.
Components
- 6″ Split Tube Conveyor
- Non-sparking Dump Cart · Batch-sized Receiving Hopper
- Explosion-proof Control Panel
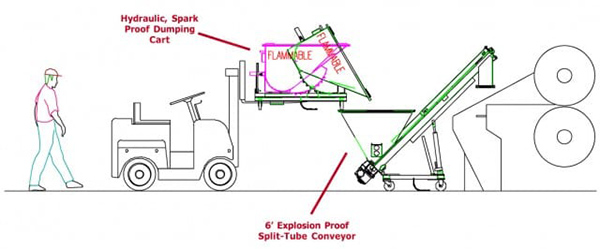
Photos and drawings are not intended to show or suggest use or non-use of any operator protection systems.
The Result
This system allows the operator to control the amount of feed to the mill, eliminating the need to manually lift 40 to 50 pounds of material. The payback in this system is to reduce lost time back injuries.